First, wire and cable classification
1, bare wires and bare conductor products
The main features of this type of product are: pure conductive metal, non-insulating and sheathing layers, such as ACSR, copper and aluminum busbars, electric locomotive lines, etc.; the processing technology is mainly pressure processing, such as smelting, rolling, pulling System, stranding/pressing and stranding, etc.; products are mainly used in suburban areas, rural areas, user main lines, switch cabinets, etc.
2, power cable
The main features of this type of product are: Extruding (wrapping) the insulation layer on the conductor, such as overhead insulated cable, or several strands (corresponding to the phase, neutral and ground of the power system), such as overhead insulation cable with more than two cores , Or increase the jacket layer, such as plastic / rubber sheathed wire and cable. The main process technologies include drawing, stranding, insulation extrusion (wrapping), cabling, armoring, sheath extrusion, etc. There are certain differences in the different process combinations of various products. The products are mainly used in the transmission of electricity, electricity, electricity, electricity, electricity and electricity in high-voltage transmission lines, with large currents (tens of amps to several thousand amps) and high voltages (220V to 500kV and above).
3, wire and cable for electrical equipment
The main features of this type of product are: variety of specifications, a wide range of applications, the use of voltage in 1kV and below, in the face of special occasions continue to derive new products, such as fire-resistant cables, flame-retardant cables, low smoke and halogen-free / low Smoke low-halogen cable, termite prevention, rat-proof cable, oil/cold resistance/temperature/wear resistance cable, medical/agricultural/mine cable, thin-walled wire, etc.
4, communication cable and optical fiber
With the rapid development of the communications industry over the past two decades, the products have also been developing at an alarming rate. From the simple telephone telegraph cable in the past to the development of thousands of pairs of voice cables, coaxial cables, optical cables, data cables, and even composite communication cables. The size of such products is usually small and uniform, and the manufacturing precision is high.
5, magnet wire (winding line)
Mainly used for various motors, instruments and meters.
Second, what need to do test certification?
Common detection items and testing purposes:
1, electrical performance testing
There are conductor direct current resistance, insulation resistance, finished product voltage test and insulated core inter-core voltage test, each of which is very important. The conductor resistance directly reflects the cable's electrical transmission performance and directly affects the temperature, life, and voltage of the cable during power on operation. Down and operational safety, it mainly examines the material and cross-sectional area of the conductor. If the material of the conductor is not good or the cross-sectional area is seriously insufficient, the DC resistance of the conductor will be seriously exceeded. This type of cable will increase the current in the circuit and increase the current. The loss caused by the passage of time causes the cable conductor itself to generate heat, causing the insulation aging of the covered conductor to crack, causing power supply circuit leakage, short circuit, and even fire, and endangering the personal and property safety. The standard has strict regulations on the DC resistance of conductors of different specifications, and must not exceed the values specified in the standard.
Insulation resistance, finished product voltage test, and insulation core voltage test, all examined the electrical insulation properties of the cable insulation layer and jacket layer, insulation resistance is to detect the resistance of the insulation material between the two conductors, it should be large enough to Insulation protection. The finished product voltage test and insulated core inter-core voltage test not only require that the cable has sufficient insulation capacity, but also that the insulating or sheathing material should be uniform and free from impurities and that the thickness is sufficiently uniform. The surface cannot have invisible trachoma, pinholes, etc., otherwise it will cause Partial breakdown during pressure test.
2, mechanical performance testing
Mainly to examine the tensile strength and elongation at break of the insulation and sheathing plastic materials, including before and after the aging, as well as the flexural and flexural tests, bending test, load breaking test, and insulated core tear test for the finished flexible cable. Static bending test. Pre- and post-aging tensile strength and elongation before and after aging are the most important and basic indicators of cable insulation and sheathing materials. They are required to be used as materials for cable insulation and sheathing, and they must not have sufficient tensile strength to pull easily. Broken, but also have a certain degree of flexibility, aging refers to the ability of insulating and sheathing materials to maintain their original performance under high temperature conditions, aging should not seriously affect the tensile strength and elongation of the material, these will have a direct impact The service life of the cable, if the tensile strength and the elongation at break are not qualified, the sheath or the insulator may be easily broken when the cable is installed and installed, or the sheath and the insulation of the cable used under the light and heat environment may be easily changed. Brittle, broken, resulting in bare exposed conductor, the risk of electric shock.
In addition, since the flexible cable is not fixedly laid and there are repeated dragging and bending in use, the flexible cable standard additionally specifies that the dynamic bending test, bending test, load breaking test, and insulated core are added to the finished cable. Tear test, static bending test, etc., to ensure that this cable meets the requirements in actual use. For example, dynamic bending and flexing test is mainly used to assess whether the flexible cable's twisted wire breaks to reduce the electrical transmission performance when the cable is subjected to external mechanical stress such as tensile and bending, or it penetrates the insulation to reduce the insulation electrical performance; It is a test method that the effect of stress is whether it deforms or cracks and affects the electrical insulation performance of the cable.
3, insulation and sheath material performance test
Including thermal weight loss, thermal shock, high temperature pressure, low temperature bending, low temperature stretching, low temperature impact, flame retardant properties and so on. These are the properties of the plastic material used to inspect the insulation and sheathing. For example, the thermal weight loss test is to measure the degree of material degradation and volatilization after aging at 80°C for 7 days; the thermal shock test is performed at a high temperature of 150°C for 1 hour after the special roll. Whether the wound insulation surface has cracks; high-temperature pressure detection of the insulation material after the high temperature and then cooling its elasticity degree; all the low temperature test generally refers to its mechanical properties at -15 °C changes, are the detection cable material in Whether it becomes brittle, easy to crack or easy to break in low temperature environment. In addition, the flame-retardant performance of the cable is very important, and the test for this performance is the non-flammability test. That is, the finished cable installed according to the standard is ignited with a special flame for a certain period of time. After the flame is extinguished by itself, the cable is checked. In the case of burning, the smaller the number of burned parts is, the better. This shows that the combustibility is poor, and the flame retardance is good and the safety is increased.
4, sign inspection
The standard requires that the cable package should be affixed with a label or logo indicating the product model, specification, standard number, name, and place of production. The specification includes the rated voltage, the number of cores, and the nominal conductor area of the conductor; the cable surface should be printed
Manufacturer's name, product type and rated voltage of continuous signs, marking spacing requirements ≤ 200mm (insulated surface) or ≤ 500mm (sheath surface), the content of the mark should be complete, clear, rub resistance, this requirement is to facilitate the user to understand the cable Model specifications and voltage levels to prevent laying errors. In addition, the wire insulation core should be preferred to use the standard recommended colors, in particular to mention the yellow / green color core, this line is generally used in the power cord of electrical products, this special two-color line dedicated to grounding, for yellow The green/green collocation standard also has the following stipulations: that is, for each segment of a long-distributed, two-color insulated wire core, one of the colors should cover at least 30% of the surface of the insulated wire core and not more than 70%, while the other color covers the insulation. The rest of the core, the yellow/green bi-color, should be basically balanced.
5, structure size detection
Including insulation and sheath thickness, the thinnest thickness, dimensions and so on. The thickness of the insulation and jacket is very important for the cable to withstand the strength of the voltage and the mechanical properties of the cable. Therefore, for different cable sizes, the standard has strict regulations on the thickness, and the requirements must not be lower than the national The standard value. Too thin cable insulation thickness will seriously affect the use of cable safety, will bring about cable breakdown, bare conductor exposed leakage and other security risks, of course, is not thicker the better, it should not affect the installation, so the standard has set a size requirements Limit this.
Common certification
1. CCC certification, mandatory certification, is a pass to enter the domestic market
2. CB certification is conducive to the export of products used in homes, offices, workshops and similar places directly related to personal safety electrical products, such products in some countries to implement mandatory certification, that is, after obtaining the country's certification certificate, It is allowed to export to the country and sell on the country’s market. Even in countries that do not have compulsory certification, consumers are willing to purchase products that have been identified as having a certification mark for their own safety.
3. CE certification is the pass for products entering the European Union and the European Free Trade Zone national market. Certified and affixed with the CE mark will reduce the risk of sales in the European market:
1) The risk of being detained and investigated by Customs;
2) Risks investigated by market surveillance agencies;
3) The risk of allegations of peers for competitive purposes.
4, UL certification, in the United States market, consumers and purchasing units are more willing to buy products with UL certification mark.
Interpretation of the New Industry Standard "Rated Voltage 0.6/1kV Aluminum Conductor Crosslinked Polyethylene Insulated Cable" (NB/T 42051-2015)
Formally implemented on September 1, 2015
In NB/T 42051-2015, compared with GBT12706-2008, the electrical type test has reduced the "insulation resistance measurement at ambient temperature" and retained the "insulation resistance measurement at the maximum temperature of the conductor during normal operation" and "4h voltage test". . The
In NB/T 42051-2015, the non-electrical type test requirements retained the GBT12706-2008 five categories of 18 testing requirements:
1, size (1 item);
2. Mechanical properties (tensile strength and elongation at break) (3 items);
3, thermoplastic properties (2 items);
4. Other types of tests (6 items);
5. No delay flame test (6 items). The
On this basis, NB/T42051-2015 added 16 new detection requirements for the following three categories:
The
1, aluminum alloy single-wire detection (4 items):
Aluminum alloy single wire tensile strength and elongation at break;
Aluminum alloy single wire bending performance;
Aluminum alloy conductor composition;
Aluminum alloy single-wire creep test. The
2. Armored layer inspection (6 items):
Inspection of the inner surface of the armored layer;
The tightness of the armor layer;
Armor layer flexibility;
Armor layer tension;
Armor layer elongation;
The thickness of the armored layer;
3, finished cable testing (6 items):
Low temperature flexibility of finished cable;
The extrusion force at room temperature;
Impact at room temperature;
Finished cable bending test;
Finished cable system connectivity test;
Salt spray test of finished cables.
Henan sanheng industrial co., LTD., founded in 2000, It is one of the top wire and cable manufacturers in China's wire and cable industry for nearly 20 years. the company has more than 5 production lines.
The production cable can be divided into more than 50 varieties and subdivided into 1000 specifications.All products have passed national certification, such as China compulsory certification, bv certification, Nigerian SONCAP certificate, China national industrial certification, etc. China national industrial production license, etc.It also has the ability to produce products that meet international standards, such as iec, ce, rohs, etc.
If you want to buy wires and cables, you can ask the customer service staff and we will get back to you as soon as possible.
-
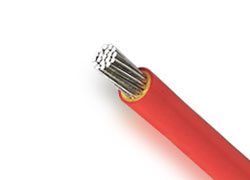
PVC Insulated Aluminum Cable
Conductor:Aluminum Conductor of Class 1/2 (Solid)
Insulation:PVC Compound
Insulation Color:Red, Blue, Green, Yellow, Brown, Black, Grey, White, Pink, Orange, Yellow/Green
-
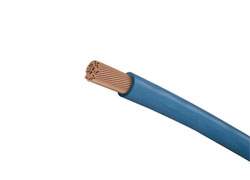
Single Core Flexible Cable
Conductor:Stranded Copper Conductor of Class 5 (Flexible)
Insulation:PVC Compound
Conductor Color:Red, Blue, Green, Yellow, Brown, Black, Grey, White, Pink, Orange, Yellow/Green
-
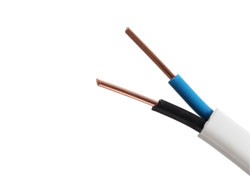
Twin and Earth Cable
Conductor:Aluminum Conductor of Class 1/2 (Solid)
Insulation:PVC Compound
Insulation Color:Red, Blue, Yellow/Green or as request
-
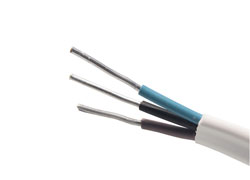
Aluminum Flat Cable
Conductor:Aluminum Conductor of Class 1/2 (Solid)
Insulation:PVC Compound
Insulation Color:Red, Blue, Yellow/Green or as request