1. Rated voltage of wire and cable products (u0/u): 300/500v
2, long-term working temperature of wire and cable is 70 °C
3, the ambient temperature when laying wire and cable is not lower than: fixed laying -40 °C, non-fixed laying -15 °C
4, the minimum bending radius of wire and cable: no armored layer should be less than 6 times the cable diameter, cable with armored layer should not be less than 12 times the cable diameter
Domestic commonly used cable technical parameters and requirements
5, wire and cable at 20 °C with DC 500v voltage test stable charge 1min after the insulation resistance should not be less than 2500mω · km
6, between the twisted pair of wire and cable and between the twist and the total should be continuous
7. The wire core and the core of the wire and cable should withstand 50hz between the core and the core. The AC 2000v voltage test will not break down for 5 minutes.
Wire and cable process flow details
1, copper, aluminum monofilament wire and cable commonly used copper, aluminum rod, at room temperature, the use of wire drawing machine through a die or several mold die hole, so that its cross-section reduced, increased length and strength. Drawing is the first process of each wire and cable company, and the main process parameter of drawing is the matching technology.
2. Monofilament Annealing Copper and aluminum monofilaments are heated to a certain temperature to increase the toughness of the monofilaments and reduce the strength of the monofilaments in a manner of recrystallization to meet the wire and cable requirements for the guidewire cores. The key to the annealing process is to eliminate the oxidation of the copper wire.
3, the stranding of the conductor In order to improve the softness of the wire and cable, in order to lay the installation, the conductive wire core is made by twisting multiple monofilaments. From the twisted form of the conductive core, it can be divided into regular twisting and irregular twisting. Irregular stranding is further divided into bundle stranding, concentric twin stranding, and special stranding. In order to reduce the occupied area of the wire and reduce the geometric size of the cable, a tightly-pressed form is adopted while the conductor is stranded, so that the ordinary round shape is mutated into a semicircle, a fan shape, a tile shape, and a tightly-pressed round shape. This type of conductor is mainly used in power cables.
Main technical requirements for plastic insulation extrusion
Eccentricity: The deviation from the extruded insulation thickness is an important indicator of the level of extrusion technology. Most of the product's structural dimensions and their deviations are clearly defined in the standard.
Smoothness: The surface of the extruded insulating layer is required to have a smooth surface, and no undesirable quality problems such as surface roughness, burnt, and impurities are allowed.
Density: The cross-section of the extruded insulation layer should be dense and solid, and must not be visible to the naked eye.
Technical requirements for cabling
The first is to prevent special-shaped insulated cores from turning over and cause twisting of the cable; second is to prevent the insulation layer from being scratched.
Most of the cables are completed with the completion of two additional processes:
One is banding to ensure that the core is not loose
The second is filling to ensure the roundness and stability of the cable after the cable is installed
Inner sheath: In order to protect the insulated wire core from being scratched by armor, proper protection of the insulating layer is required;
The inner cover points: squeeze the inner cover (separation sleeve) and wrap the inner cover (cushion). Replacing the lashing band around the cushion layer and the cabling process;
Domestic commonly used cable technical parameters and requirements
Mounting: Laying in underground cables, the work may be subject to a certain positive pressure effect, the choice of steel strip armored structure. When the cable is laid in a place where there is both positive pressure and tensile force, the structure with internal steel wire armor should be used.
Outer Sheath: The portion of the structure that protects the insulation of the wire and cable from environmental factors. The main role of the outer sheath is to improve the mechanical strength of the wire and cable, prevent chemical corrosion, moisture, water leaching, and prevent the cable from burning. According to the different requirements of the cable, the plastic jacket is directly squeezed by the extruder.
Henan Sanheng Industrial Co., Ltd. , founded in 2000, It is one of the top wire and cable manufacturers in China's wire and cable industry for nearly 20 years. the company has more than 5 production lines., founded in 2000, It is one of the top wire and cable manufacturers in China's wire and cable industry for nearly 20 years. the company has more than 5 production lines.
The production cable can be divided into more than 50 varieties and subdivided into 1000 specifications.All products have passed national certification, such as China compulsory certification, bv certification, Nigerian SONCAP certificate, China national industrial certification, etc. China national industrial production license, etc.It also has the ability to produce products that meet international standards, such as iec, ce, rohs, etc.
If you want to buy wires and cables, you can ask the customer service staff and we will get back to you as soon as possible.
-
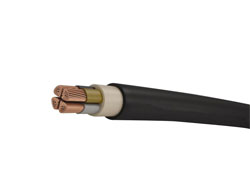
600-1000V CU XLPE Power Cable
Conductor:Bare Copper Conductor of Class 1/2 (Solid)
Insulation:XLPE Compound
Insulation Color:Red, Blue, Grey, Yellow/Green or as request
-
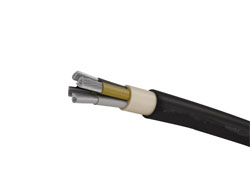
600-1000V AL XLPE Power Cable
3500 V:Bare Aluminum Conductor of Class 1/2 (Solid)
Insulation:XLPE Compound
Insulation Color:Red, Blue, Grey, Yellow/Green or as request
-
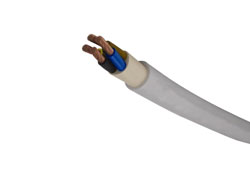
600-1000V Flexible Power Cable
Conductor:Bare Copper Conductor of Class 5 (Flexible)
Insulation:PVC Compound
Insulation Color:Red, Blue, Grey, Yellow/Green or as request
-
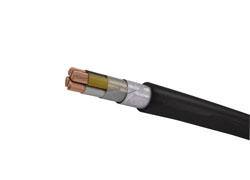
600-1000V SWA Armoured Cable
Conductor:Bare Copper Conductor of Class 1/2 (Solid)
Insulation:XLPE Compound
Insulation Color:Red, Blue, Grey, Yellow/Green or as request